Présentation du four à chaux Pierre Méralikan
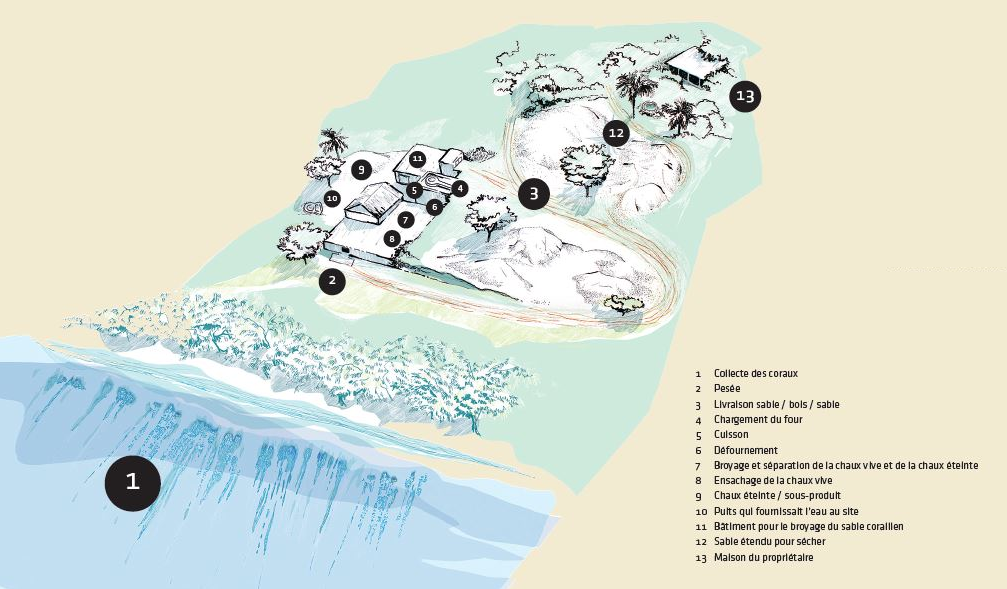
Construit dans la seconde moitié du XIXe siècle, fermé en 1995, il a la particularité d’être le dernier des fours à chaux réunionnais. À ce titre, il est inscrit Monument Historique.
Le four « à feu continu » n’a pas été modifié jusqu’à sa fermeture. Un nouveau broyeur est installé en 1967. L’ancien est toujours visible.
Sur le plan technologique, ce four à chaux hérite des savoir-faire accumulés par toute une lignée de chaufourniers depuis des millénaires à travers les continents.
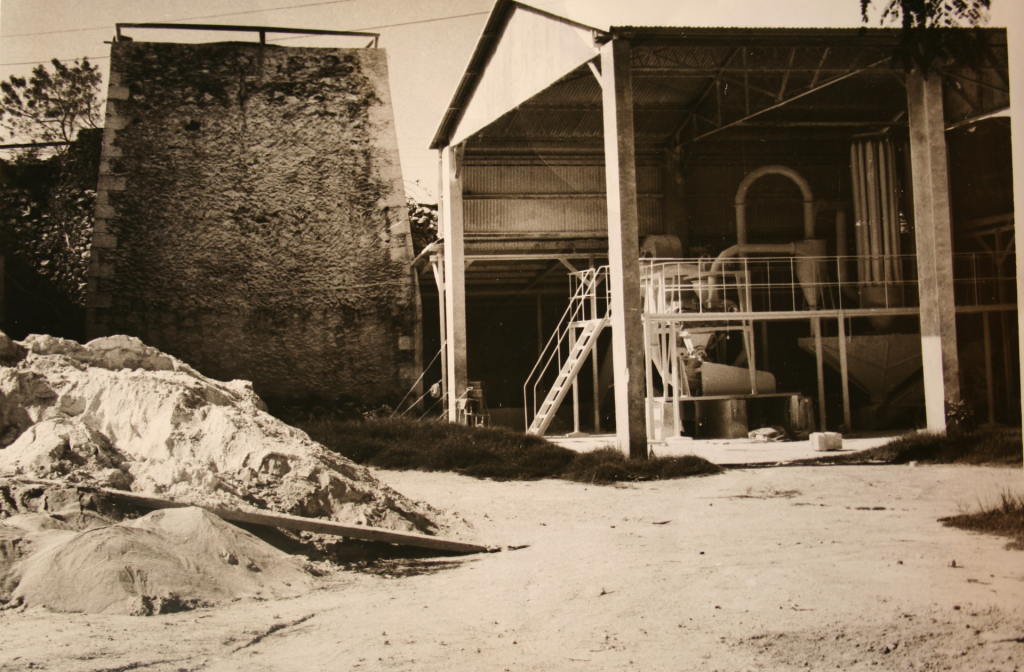
Le dernier des fours à chaux
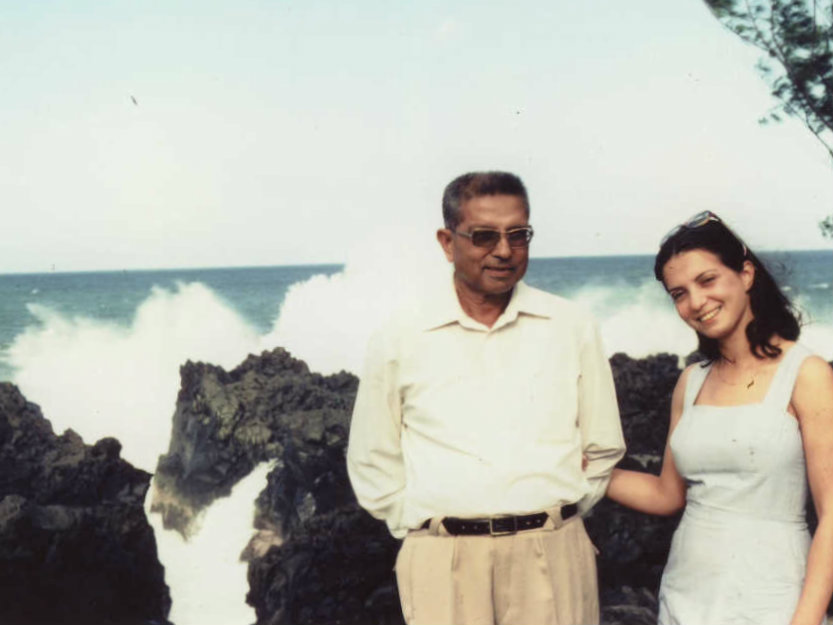
La chaux réunionnaise est florissante et essentielle à l’île jusqu’après la seconde guerre mondiale. À partir des années 1960, son déclin est assez radical pour plusieurs raisons :
- La chaux importée revient moins chère que celle produite localement dès que l’embargo prend fin.
- Le béton devient le produit phare dans les constructions.
- La barrière corallienne s’est fortement dégradée par des siècles de collecte soutenue. En 1969, le préfet prend alors un arrêté interdisant la collecte des coraux dans le lagon.
La majeure partie des fours à chaux de l’île cesse alors de fonctionner. Pour continuer son activité, Pierre Méralikan adopte une double stratégie :
- Il diversifie son activité en fabricant une nouvelle unité de broyage de sable pour obtenir du calcaire servant à l’amendement des sols.
- Il se fournit en coraux ramassés sur les plages et dans les stocks des fours à chaux fermés.
Ce four à chaux a longtemps pallié, seul, aux déficiences des importations en période de campagne sucrière. Il produisait environ 2 500 tonnes de chaux par an.
Dans les années 1990, l’administration lui demande de fermer son usine. Pierre Méralikan le fait en 1995, avant même d’avoir pu épuiser son stock de corail.
Chronologie des propriétaires
- Date non connue : Pierre Guy LESPORT
- Date non connue : Ernest MAZEAU
- 31 octobre 1886 : Céline Ernestine MAZEAU veuve de Léopold DELTEL
- 18 septembre 1914 : Henri Bertin Ortaire BEGUE
- 17 avril 1950 : Jean Michel Raphaël MERALIKAN
- 2 janvier 1953 : Emilien Pierre MERALIKAN
(Source : conservatoire des hypothèques)
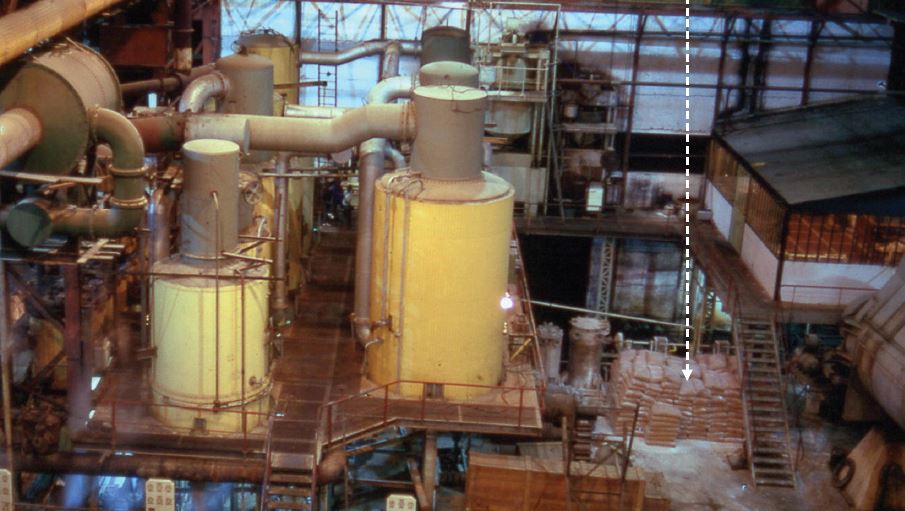
La collecte des coraux
Jusqu’en 1969…
Le ramassage de blocs de madrépores (corail en forme de tête de mort) s’effectue à marée basse à l’aide d’un radeau appelé « jingade » -prononcé « zingade»- fait en hampes (8 à 12) de chokas séchées et assemblées par des tringles en bois de filaos.
Les casseurs de coraux sont vêtus d’un caleçon dit « moresse », de chaussures confectionnées dans une section de pneu percée de plusieurs trous côté jante, reliés par une ficelle.
Le casseur de coraux monte sur le zingade et le déplace à l’aide d’une gaule plantée dans le sable.
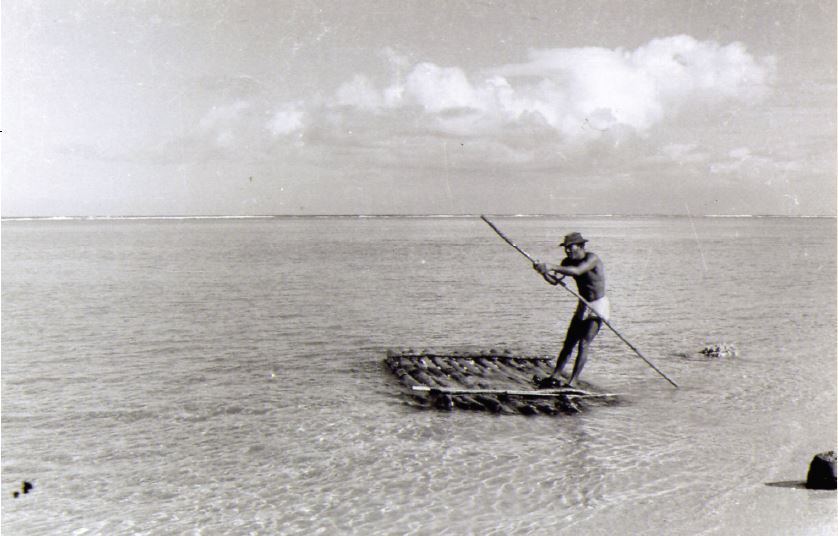
Il descend du zingade. Muni d’une grande barre à mines, il casse les gros coraux « tête de mort » qui contient le plus de calcaire. Il les dépose sur le radeau.
Lorsque le zingade est rempli de coraux, il est tiré à pied jusqu’à la plage pour être déchargé.
Les blocs de madrépores sont mis à sécher sur la plage. Des camions viennent ensuite les récupérer pour les livrer au pied de la gueule du four.
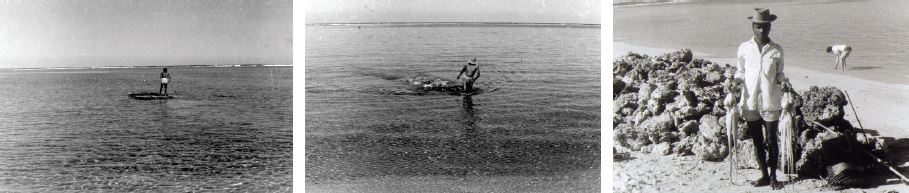
Après 1969
Devant la destruction massive du lagon, le préfet Vaudeville interdit la récolte du corail dans les lagons par arrêté du 9 juin 1969. À partir de cette date, la majorité des fours à chaux de l’île cesse de fonctionner. Pour se fournir en coraux, Pierre Méralikan souscrit aux conditions de concession accordée par l’État. Il a le droit d’exploiter les coraux ramassés sur la plage et de récupérer ceux stockés dans les autres fours à chaux.
La gueule du four
Le chargement du four s’effectue par le gueulard en couches alternées de bois et de coraux. Une couche de bois + une couche de coraux forment un « piquet ». Pour remplir le four, il faut environ 600 kg de bois de tamarin pour 500 kg de corail (30 paniers).
Pierre Méralikan commandait du bois livré prédécoupé à la dimension de la largeur intérieure du four.
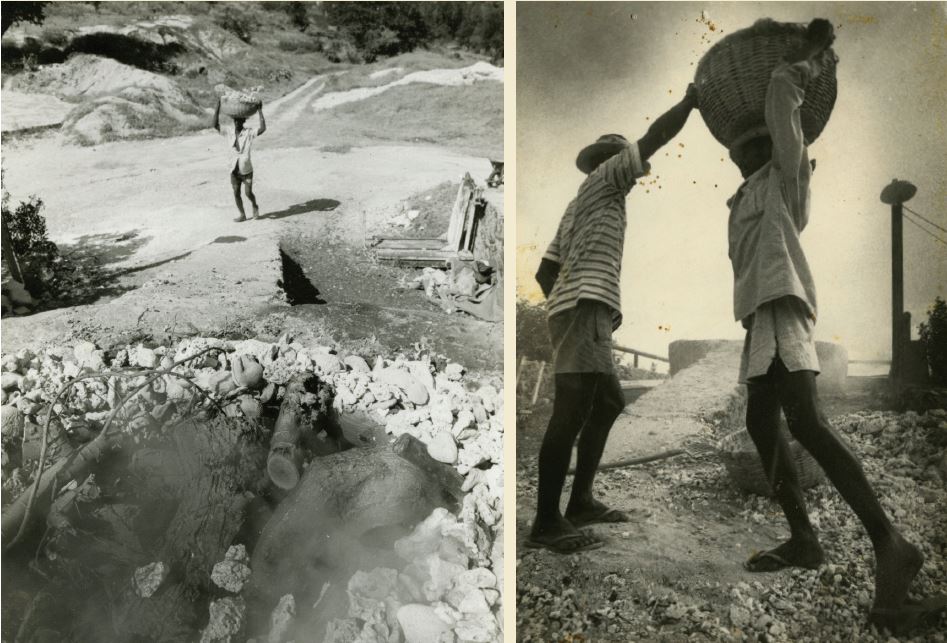
Le four
Le four est chargé en couches alternées de bois et de corail jusqu’à un mètre en butée au-dessus de la gueule du four.
Le bois, allumé en partie basse, se consume à 800°C en cuisant la couche de coraux lui succédant. Le four est rechargé en continu durant toute la période. Une colonne se cuit sur un peu moins d’une journée.
Le défournement et étalage des coraux cuits
1- Le défournement se décide au jugé, d’après la chaleur qui se dégage autour du four.
Les blocs de chaux vive sont retirés par l’orifice d’allumage du four, à l’aide de pelles.
Ils sont chargés dans une brouette puis étalés en ligne avec un râteau.
2- On les arrose d’un seau d’eau rempli au puits situé à l’entrée du site. Grâce à l’humidité ambiante de l’air, une petite quantité d’eau suffit pour que la chaux vive se délite. On dit alors que le corail « s’ouvre ».
3- On obtient une poudre semi-éteinte. Elle est chargée sur le tapis du broyeur.
L’unité de broyage
Le broyeur assure la transformation de la chaux en poudre très fine. Installé en 1967, il permet d’obtenir une fleur de chaux de grande qualité achetée par les usines sucrières pour clarifier le jus de canne. La chaux semi-éteinte est entraînée par une chaîne sans fin jusqu’au broyeur.
Le cyclone séparateur isole deux produits : la chaux éteinte et la chaux vive (« fleur de chaux »).
La chaux éteinte ressort par un tuyau. Elle est récupérée à la brouette, stockée à l’air libre et arrosée une deuxième fois. Elle devient un sous-produit vendu pour l’amendement des sols et en complément dans l’alimentation animale.
La chaux vive, plus légère, est expulsée dans les tuyaux. Le produit fini est séparé de l’air sur un filtre à manche (appelé « chemise » par Pierre Méralikan) et mis en sacs de 50 kg manuellement par ensacheuse.
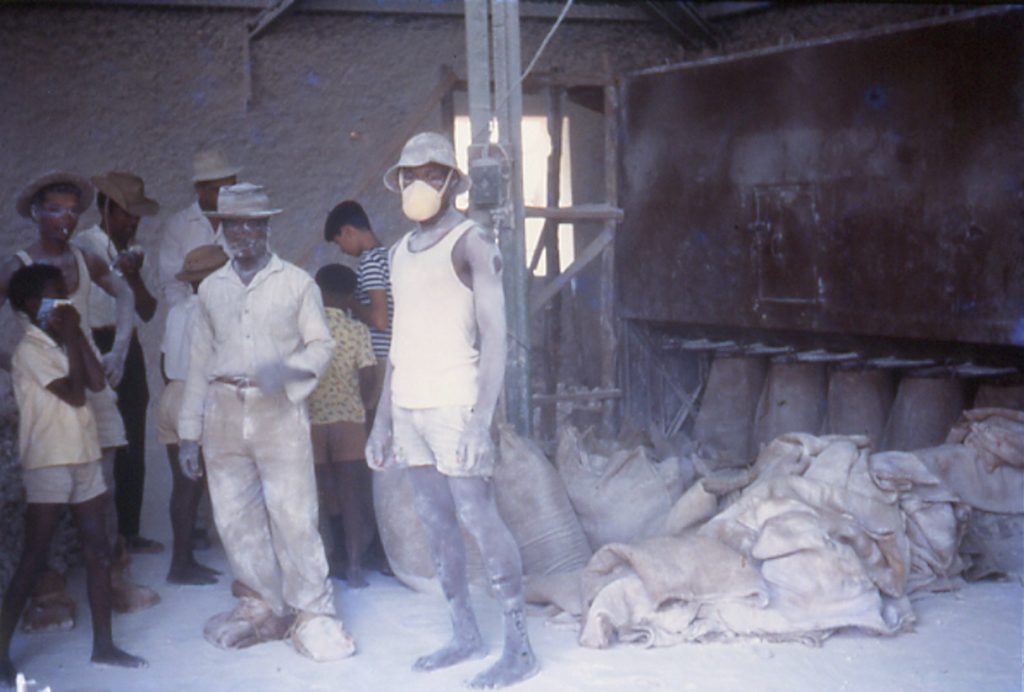
La pesée et la livraison
Les camions arrivent sur le plateau extérieur de la bascule relié à la balance située à l’intérieur. La balance pèse tout aussi bien les matières premières entrant, bois et coraux, que la chaux et le calcaire sortant de l’usine. Les camions vont ensuite livrer bois ou corail sur la plateforme située au niveau de la gueule du four.
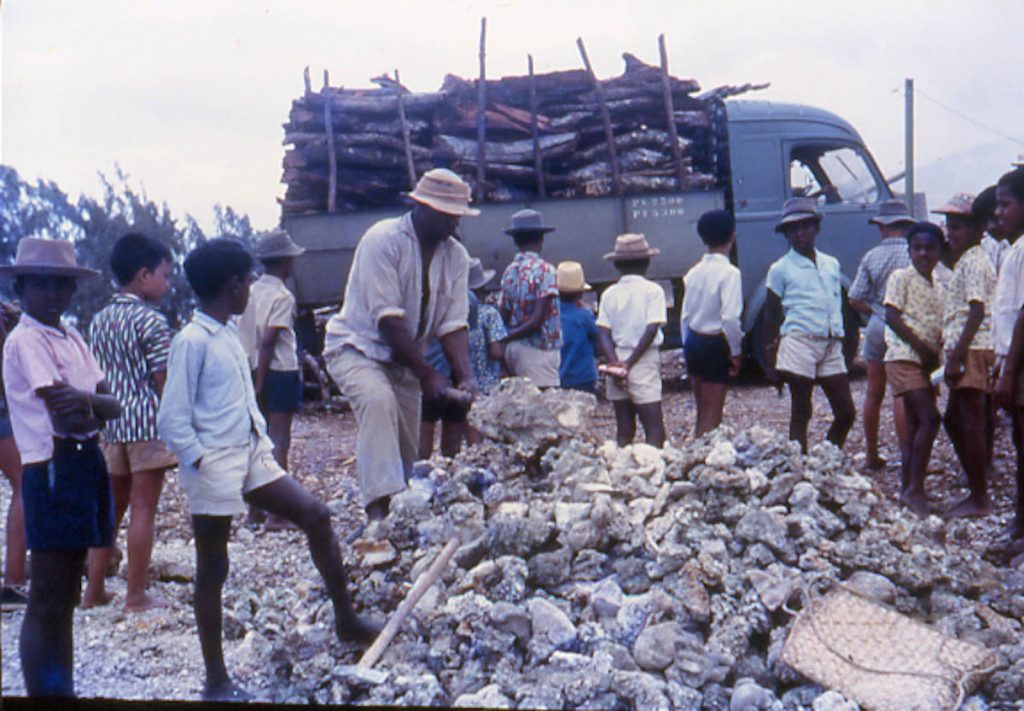
La vie au four à chaux
Entre 6 et 8 personnes travaillent à la petite usine. Le broyage et l’ensachage s’effectuent surtout la nuit, pour que l’usine dispose de suffisamment d’électricité pour fonctionner.
La paie des ouvriers se fait chaque samedi après-midi. Il était courant que le patron fasse des avances sur salaire. Il était de coutume à l’époque que les ouvriers bénéficient d’une sorte de supplément, au choix : du rhum ou du lait de la ferme de Pierre Méralikan située au Tévelave !
La chaux extrêmement corrosive impose des mesures de protection drastiques pourtant « réadaptées » aux spécificités locales …
Les « chaussures de protection » : les ouvriers ne portent que des savates (tongs) dans leur quotidien. D’autres sont pieds nus. Les protections des pieds sont constituées d’une dizaine d’épaisseurs de toile de « gonis » (jute) neufs remontée autour des chevilles, attachée au bout par une corde. Ces « chaussures » sont confectionnées chaque jour tant la corrosion est importante.
Les masques de protection pour prévenir de la silicose : Pierre Méralikan importe des masques pour réduire l’inhalation de particules nocives pour la santé. Jean-Louis Méralikan, le fils nous a raconté l’anecdote suivante : Lorsque mon père leur a demandé de porter les masques pour ne pas avoir la silicose, certains ont interprété qu’il s’agissait d’un moyen de leur interdire de parler. » En effet, en créole « si li koz » (silicose) signifie « s’il parle » ! En conséquence, certains refusent de porter des masques qu’ils remplacent parfois par des mouchoirs attachés autour du nez.
Souvenirs de Guylène Méralikan, la fille de Pierre :
« Mon père mettait des bouteilles d’huile de coco à la disposition de ses ouvriers. Ils l’utilisaient, outre le savon, pour bien nettoyer et nourrir leur peau. Ils en mettaient aussi dans les cheveux. En effet, avec la chaux, la chaleur ajoutée à l’humidité ambiante… il fallait bien ça ! »
« Pendant la campagne sucrière… il y avait un ouvrier, toujours le même, car il le souhaitait, qui concassait les coraux durant la nuit. Mon père avait fait mettre un bec de lumière sur la « gueule du four ». On entendait alors depuis notre maison, sur fond du bruit des vagues qui se brisaient sur le récif de la mer, le « tac…tac » sec du concassage ».
Le chargement du sable
Après l’arrêté préfectoral de 1969 interdisant la collecte de coraux, Pierre Méralikan décide de diversifier son activité. Il met en place cette unité de broyage de sable corallien qui fonctionne lorsque le four à chaux est inactif – hors campagne sucrière -.
À l’emplacement de l’actuelle route, le sable est étendu au soleil durant toute la matinée pour le sécher. En début d’après-midi, il est pelleté et vidé dans la cabane abritant un grand tamis duquel le sable s’écoule pour être broyé, durant la nuit, par la machine installée dans le bâtiment au-dessous. On obtient de la poudre de calcaire utilisée pour amender les sols agricoles acides, en complément de l’alimentation animale et dans les constructions.
La production de calcaire broyé
Cette installation secondaire produit du calcaire corallien à partir de sable broyé.
L’intérieur de cette machine est simplement rempli de billes de métal qui broyaient le sable en farine. Le calcaire produit est vendu pour l’amendement agricole et l’alimentation du bétail (calcium). Il sert également à la construction après être mélangé à la chaux.
Cette machine produisait annuellement environ 5 000 tonnes de calcaire.
Petite histoire de four à chaux à La Réunion
En Europe, la chaux est utilisée dans la construction depuis des siècles. À La Réunion, la Compagnie française des Indes orientales décide d’en fabriquer, dès les premiers pas de la colonisation en 1664, pour construire les bâtiments en dur. À la fin du XIXe siècle, les usines de fours à chaux prennent de l’ampleur. La chaux devient une activité à part entière. Apparaît le métier de « chaufournier ».
La chaux se mêle alors étroitement à l’évolution de l’île :
- Elle est un élément important dans la construction des bâtiments en dur dont de nombreuses églises et des bâtiments administratifs coloniaux.
- Elle alimente les grands travaux dans l’île tels que la construction du chemin de fer de La Réunion de 1872 à 1886.
À Saint-Leu, la chaux fabriquée localement intervient dans un grand nombre de constructions : le pont des Colimaçons construit en moellons liés par de la chaux, le viaduc de la Petite Ravine, le Pont de la Grande-Ravine, l’enceinte du cimetière blanchie à la chaux, l’ancien entrepôt de maïs et de café (devenu l’Hôtel des postes).
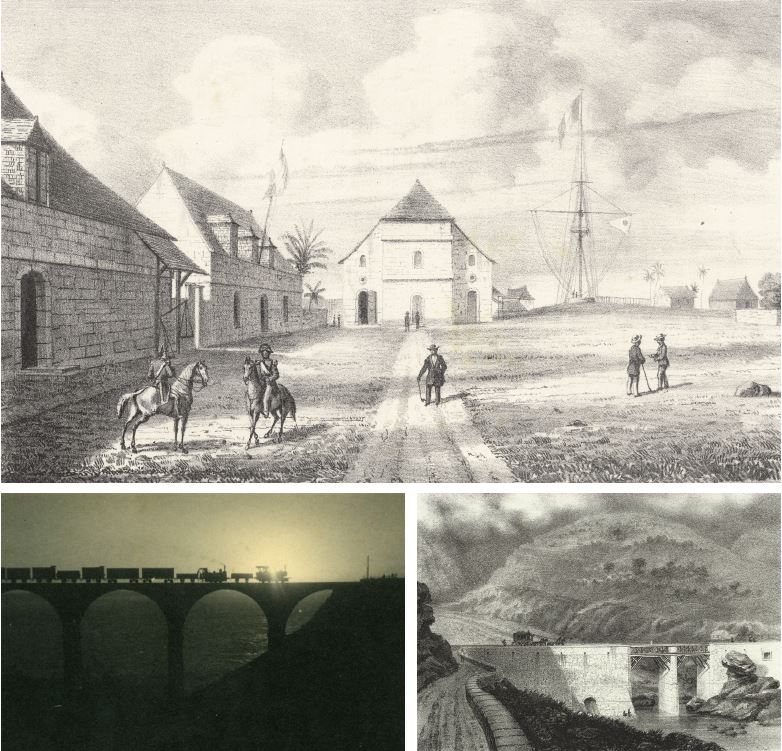
Les utilisations de la chaux
Depuis le début de la colonisation jusqu’à la fin de la seconde guerre mondiale, la chaux a été un produit familier et totalement intégré au quotidien des Réunionnais. Son utilisation est multiple :
Pour le mortier de construction
Au tout début de la colonisation, la chaux sert essentiellement dans la construction. Mélangée au sable, elle participe à l’élaboration des mortiers et des enduits, pour toutes sortes de constructions (murs, ponts).
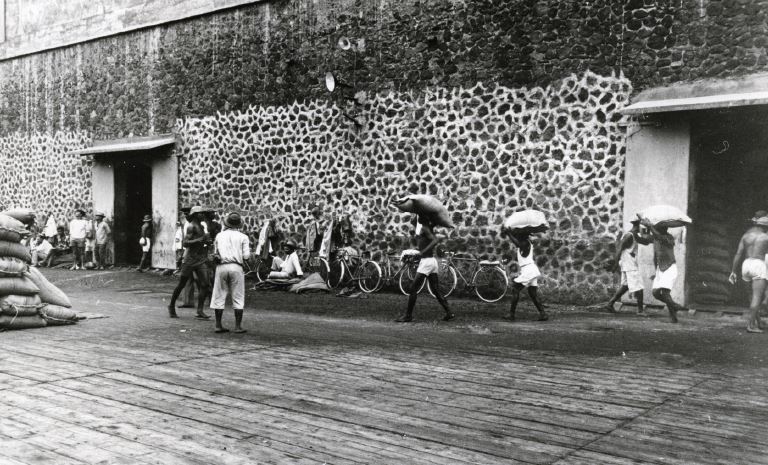
Pour épurer le jus de canne
Dans les sucreries, la chaux intervient au moment du raffinage. Cette opération est appelée « chaulage ». La chaux est rajoutée au jus de canne chauffé. Elle agit alors comme une «lessive» : les acides contenus dans le jus sont transformés en sels insolubles et les matières albuminoïdes coagulent. Le précipité obtenu se décante après chauffage. On obtient de « écumes » ou « tourteaux » qui deviennent d’excellents engrais.
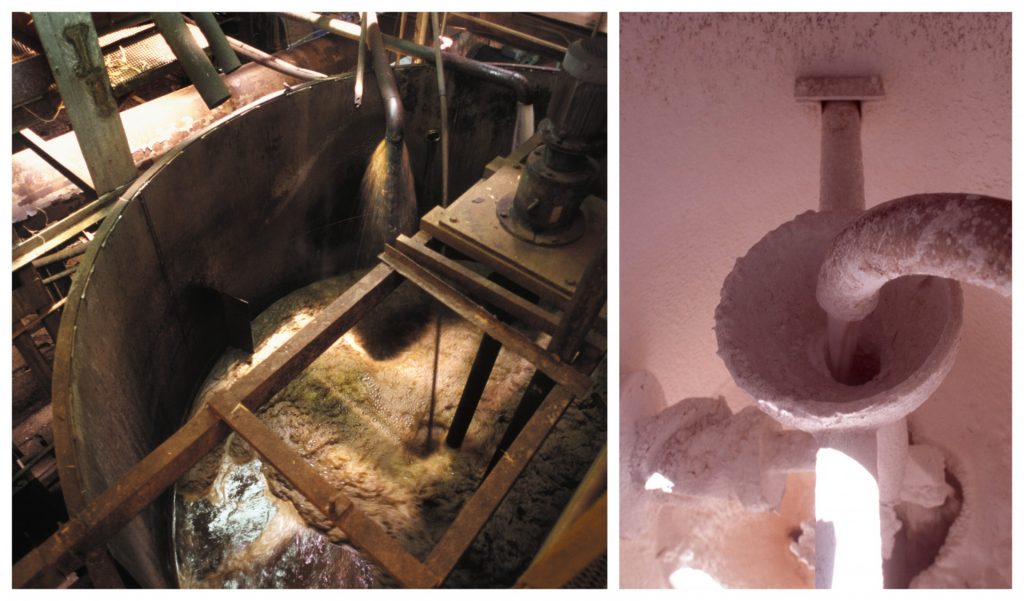
Pour désinfecter
La chaux est particulièrement hydrophile. Elle est utilisée pour assécher, détruire les matières organiques riches en eau. La chaux a été utilisée comme désinfectant à La Réunion. Pendant la grippe espagnole en 1919, les morts sont jetés dans les fosses communes et recouverts d’une couche de chaux. Une couche de morts, une couche de chaux, une couche de chaux, une couche de morts…
Dans son livre intitulé « Les fours à chaux de La Réunion » Georges Tergémina écrit : « la chaux était le crayon à grand format de l’île à l’époque, elle servait entre autres à guérir les maux de ventre !… ».
Pour amender les sols trop acides
La chaux a longtemps servi à l’amendement des terres trop acides.
Chaux, corail et bois : histoires de déclin
La chaux se fabrique à partir de calcaire. Or, l’île, de formation exclusivement volcanique, ne dispose d’aucun gisement. La matière première nécessaire à la fabrication de la chaux n’est issue que des seules formations coralliennes de seulement 25km de côtes !
Par ailleurs, la cuisson des coraux exige d’importantes quantités de bois. Une très grande partie de la forêt primaire va ainsi disparaître pour satisfaire les besoins toujours plus grands de l’économie locale.
De 1884 à 1945, la chaux corallienne locale est exploitée de manière intensive
Lorsque le chemin de fer fonctionne à partir de 1884, l’utilisation de la chaux s’étend à la côte Est. Jusqu’à la création du port de la Pointe des Galets en 1886, on utilise exclusivement la chaux fabriquée localement. Les importations sont considérablement ralenties lors de la première guerre mondiale (1914-1918) et totalement inexistantes durant la seconde (1939-1945) à cause du blocus.
À partir de 1945, plusieurs paramètres vont inverser la tendance :
- La chaux industrielle importée devient très concurrentielle malgré les frais de transports.
- La demande se fait moins grande de la part de l’industrie sucrière frappée par le borer (insecte parasite de la canne), trois forts cyclones et la baisse des cours.
- À partir de 1960, on entre dans l’ère du béton.
Enfin, devant la destruction massive du lagon, le préfet Vaudeville interdit la récolte du corail dans les lagons par arrêté n° I.1486 du 9 juin 1969.
Le four à chaux Pierre Méralikan résistera encore quelques décennies, parce qu’il souscrit aux conditions de concession accordée par l’État. Il a le droit d’exploiter les coraux ramassés sur la plage et de prélever du sable corallien dans les dunes.
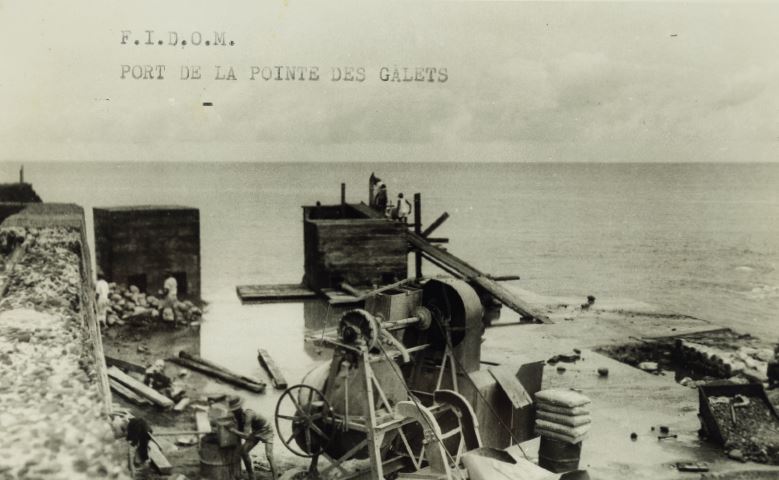
Vous pouvez visiter le four à chaux Pierre Méralikan à Saint-Leu. ► + d’infos
Exposition permanente installée dans les vestiges restaurés du four à chaux Pierre Méralikan, propriété du TCO -Territoire de la Côte Ouest – communauté d’agglomération
Recherches, conception et rédaction : Geneviève Pothin
Graphisme et scénographie : Pascal Knoepfel – Atelier Crayon Noir
Illustratrice : Solen Coeffic
Impression, fabrication et installation : Réuni Pub